Нержавеющая сталь – это разнови сайтдность легированной стали, устойчивая к коррозии за счет содержания хрома – 12% и более. В присутствии кислорода образуется оксид хрома, который создает на поверхности стали инертную пленку, защищающую все изделие от неблагоприятных воздействий. Современный рынок может предложить различные марки нержавеющей стали для применения в самых разных отраслях промышленности.
Не каждая марка нержавеющей стали демонстрирует устойчивость хромоксидной пленки к механическим и химическим повреждениям. Хотя пленка восстанавливается под воздействием кислорода, были разработаны специальные марки нержавейки для применения в агрессивных средах.
В России развита сталелитейная промышленность и существуют собственные обозначения для марок стали, однако самые популярные марки имеют зарубежные аналоги. Это стали так называемых 300-й и 400-й серий, которые отличаются высокими характеристиками коррозионной стойкости, устойчивости к агрессивным средам, пластичности и прочности. Они практически универсальны и применяются для производства самой разнообразной продукции – от медицинских инструментов до крупных строительных конструкций. 200-я серия постепенно догоняет их по популярности за счет выгодного соотношения цена-качество.
Виды стали 300-й серии
Хромникелевая нержавейка этой группы по своему химическому составу бывает аустенитная, аустенитно-ферритная и аустенитно-мартенситная, в зависимости от процентного содержания углерода, никеля, хрома и титана. Это самая универсальная нержавейка, свойства которой обеспечивают ей неизменно высокий спрос на рынке.
AISI 304 (08Х18Н10)
Востребованная во всех отраслях промышленности, эта нержавейка, однако, снискала славу «пищевой». Ее химический состав и свойства делают ее наиболее подходящей для применения в пищепроме. Она легко поддается сварке, показывает высокие характеристики коррозийной стойкости в агрессивных средах. Ее также часто выбирают для химической, фармацевтической, нефтяной и текстильной промышленности.
AISI 316 (10Х17Н13М2)
Нержавейка 316 получается, если добавить в 304-ю нержавейку молибден, что еще больше повышает коррозионную устойчивость и способность к сохранению свойств в агрессивных кислотных средах, а также при высоких температурах. Эта нержавеющая сталь дороже, чем 304, она используется в химической, нефтегазовой и судостроительной промышленности.
AISI 316T (10Х17Н13М2Т)
Эта марка стали нержавейки содержит небольшое количество титана, повышающего прочность материала, делающего его устойчивым к высоким температурам, а также к ионам хлора. Используется в сварных конструкциях, для изготовления лопастей газовых турбин, в пищевой и химической промышленности. Доступная цена и высокие технические характеристики делают эту нержавеющую сталь очень популярной.
AISI 321 (12-08Х18Н10Т)
Нержавеющая сталь, характеристики которой обусловлены повышенным содержанием титана. Легко поддается сварочной обработке, устойчива к температуре до 800 o С. Широко востребована для изготовления бесшовных труб, а также трубопроводных фитингов — фланцев, тройников, отводов и переходов.
Цветные металлы и сплавы: классификация, ассортимент и свойства
Цветные металлы и сплавы: классификация, ассортимент и свойства.
К цветным металлам относятся все металлы, кроме железа и сплавов на его основе – сталей и чугунов, которые называются черными. Сплавы на основе цветных металлов используют в основном как конструкционные материалы со специальными свойствами: коррозионно-стойкие, подшипниковые (обладающие низким коэффициентом трения), тепло- и жаропрочные и др.
В маркировке цветных металлов и сплавов на их основе нет единой системы. Во всех случаях принята буквенно-цифровая система. Буквы указывают на принадлежность сплавов к определенной группе, а цифры в разных группах материалов имеют разное значение. В одном случае они указывают на степень чистоты металла (для чистых металлов), в другом – на количество легирующих элементов, а в третьем обозначают номер сплава, которому по гос. стандарту должны соответствовать определенный состав или свойства.
Медь и ее сплавы
Техническая медь маркируется буквой М, после которой идут цифры, связанные с количеством примесей (показывают степень чистоты материала). Медь марки М3 содержит примесей больше, чем М000. Буквы в конце марки означают: к – катодная, б – безкислородная, р – раскисленная. Высокая электропроводность меди обуславливает ее преимущественное применение в электротехнике как проводникового материала. Медь хорошо деформируется, хорошо сваривается и паяется. Ее недостатком является плохая обрабатываемость резанием.
К основным сплавам на основе меди относятся латуни и бронзы. В сплавах на основе меди принята буквенно-цифровая система, характеризующая химический состав сплава. Легирующие элементы обозначаются русской буквой, соответствующей начальной букве названия элемента. Причем часто эти буквы не совпадают с обозначением тех же легирующих элементов при маркировке стали. Алюминий – А; Кремний – К; Марганец – Мц; Медь – М; Никель – Н; Титан –Т; Фосфор – Ф; Хром –Х; Бериллий – Б; Железо – Ж; Магний – Мг; Олово – О; Свинец – С; Цинк - Ц.
Порядок маркировки литейных и деформируемых латуней разный.
Латунь - сплав меди с цинком (Zn от 5 до 45%). Латунь с содержанием от 5 до 20% цинка называется красной (томпаком), с содержанием 20–36% Zn – желтой. На практике редко используют латуни, в которых концентрация цинка превышает 45%. Обычно латуни делят на:
- двухкомпонентные латуни или простые, состоящие только из меди, цинка и, в незначительных количествах, примесей;
-многокомпонентные латуни или специальные – кроме меди и цинка присутствуют дополнительные легирующие элементы.
Деформируемые латуни маркируются по ГОСТ 15527-70.
Марка простой латуни состоит из буквы «Л», указывающей тип сплава - латунь, и двузначной цифры, характеризующей среднее содержание меди. Например, марка Л80 - латунь, содержащая 80 % Cu и 20 % Zn. Все двухкомпонентные латуни хорошо обрабатываются давлением. Их поставляют в виде труб и трубок разной формы сечения, листов, полос, ленты, проволоки и прутков различного профиля. Латунные изделия с большим внутренним напряжением (например, нагартованные) подвержены растрескиванию. При длительном хранении на воздухе на них образуются продольные и поперечные трещины. Чтобы избежать этого, перед длительным хранением необходимо снять внутреннее напряжение, проведя низкотемпературный отжиг при 200-300 C.
В многокомпонентных латунях после буквы Л пишут ряд букв, указывающих, какие легирующие элементы, кроме цинка, входят в эту латунь. Затем через дефисы следуют цифры, первая из которых характеризует среднее содержание меди в процентах, а последующие - каждого из легирующих элементов в той же последовательности, как и в буквенной части марки. Порядок букв и цифр устанавливается по содержанию соответствующего элемента: сначала идет тот элемент, которого больше, а далее по нисходящей. Содержание цинка определяется по разности от 100%.
Латуни в основном применяются как деформируемый коррозионно-стойкий материал. Из них изготавливают листы, трубы, прутки, полосы и некоторые детали: гайки, винты, втулки и др.
Литейные латуни маркируются в соответствии с ГОСТ 1711-30. В начале марки тоже пишут букву Л (латунь), после которой пишут букву Ц, что означает цинк, и число, указывающее на его содержание в процентах. В легированных латунях дополнительно пишут буквы, соответствующие введенным легирующим элементам, и следующие за ними числа указывают на содержание этих элементов в процентах. Остаток, недостающий до 100 %, соответствует содержанию меди. Литейные латуни используют для изготовления арматуры и деталей для судостроения, втулок, вкладышей и подшипников.
Бронзы (сплавы меди с различными элементами, где цинк не является основным). Они подобно латуням подразделяются на литейные и деформируемые. Маркировка всех бронз начинается с букв Бр, что сокращенно означает бронза.
В литейных бронзах после Бр пишут буквы с последующими цифрами, которые символически обозначают элементы, введенные в сплав (в соответствии с таблицей 1), а последующие цифры обозначают содержание этих элементов в процентах. Остальное (до 100 %) – подразумевается медь. Иногда в некоторых марках литейных бронз в конце пишут букву «Л», что означает литейная.
Большинство бронз обладает хорошими литейными свойствами. Их применяют для различного фасонного литья. Чаще всего их используют как коррозионно-стойкий и антифрикционный материал: арматура, ободы, втулки, зубчатые колеса, седла клапанов, червячные колеса и т.д. Все сплавы на основе меди имеют высокую хладостойкость.
Алюминий и сплавы на его основе
Алюминий выпускают в виде чушек, слитков, катанки и т.п. (первичный алюминий) по ГОСТ 11069-74 и в виде деформируемого полуфабриката (листы, профили, прутки и т.п.) по ГОСТ 4784-74. По степени загрязненности тот и другой алюминий подразделяется на алюминий особой чистоты, высокой чистоты и технической чистоты. Первичный алюминий по ГОСТ 11069-74 маркируют буквой А и числом, по которому можно определить содержание примесей в алюминии. Алюминий хорошо деформируется, но плохо обрабатывается резанием. Прокаткой из него можно получить фольгу.
Нержавейка для пищевой промышленности – марки стали и характеристики
Пищевая нержавеющая сталь – это вид стального сплава, который активно применяется в различных отраслях промышленности. Такую популярность материал завоевал благодаря своим физическим и химическим свойствам, привлекательному внешнему виду и высокой степени прочности.
Основные сферы применения пищевой нержавейки
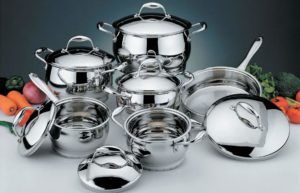
Утварь из нержавеющей стали
Из металлических листов нержавеющего сплава изготавливаются столовые приборы, кастрюли, противни для духовок, корпуса холодильников, плит и других предметов бытовой домашней техники. Помимо утвари, без этого материала не обходится ни одно предприятие, занятое в производстве, хранении или переработке пищевых продуктов: многие элементы оборудования на заводах, которые сортируют, смешивают и измельчают сырьё, сделаны из нержавеющей стали.
Область использования нержавейки стремительно расширяется, и это неудивительно: посуда из нержавейки отличается своей износостойкостью, долговечностью и простотой ухода. Материал подходит для домашней консервации, разнообразной термической обработки и хранения пищевой продукции.
Чем отличается от обычной нержавеющей стали
Основная характеристика, благодаря которой можно отличить материал от обычных нержавеющих стальных сплавов – это высокая коррозийная устойчивость. Необходимый показатель достигается при помощи высокого – до 27% – содержания в составе хрома. Этот химический элемент способствует образованию специальной окисной плёнки.
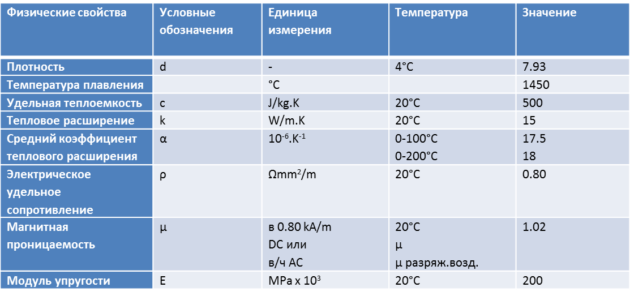
Таблица физических свойств нержавеющей стали
Алюминий и его сплавы
СВОЙСТВА И ПРИМЕНЕНИЕ АЛЮМИНИЯ
По объему производства и масштабам применения алюминий (Аl) является самым распространенным цветным металлом. Он открыт в 1826 г. Его название происходит от латинского слова «алюмен» —название квасцов (соединения, содержащего алюминий).
Алюминий имеет относительно малую плотность, низкую температуру плавления (658°С) и очень высокую скрытую теплоту плавления. Он хорошо поддается механической обработке: прокатке, ковке, волочению, резанию и т. п., а также обладает высокой теплопроводностью и электропроводностью. Электропроводность алюминия составляет 60—65% от электропроводности меди. Алюминий в три раза легче меди, поэтому алюминиевый провод с таким электросопротивлением легче, чем медный. Обладая большим сродством к кислороду, алюминий имеет одновременно и высокую коррозионную стойкость на воздухе и в ряде других сред.
Чистый алюминий имеет малую прочность и не может быть использован в качестве конструкционного материала. Однако прочность его резко возрастает под влиянием добавок других элементов, термической и механической обработки. Многие сплавы на основе алюминия обладают достаточно высокой механической прочностью, сочетающейся с малой плотностью, что делает их весьма ценным конструкционным материалом.
Алюминий и алюминиевые сплавы служат весьма эффективными заменителями свинца, меди, олова, цинка, а в ряде случаев их успешно используют вместо стали. В электротехнике алюминий применяют для изготовления проводов, кабелей, шинопроводов, конденсаторов, выпрямителей переменного тока и т. д. Алюминиевые сплавы широко применяют в литом и деформированном состояниях в различных авиаконструкциях, в транспортном машиностроении и автомобильной промышленности. Благодаря высокой коррозионной стойкости алюминий применяют в химическом машиностроении при изготовлении аппаратуры для производства азотной кислоты, органических веществ, пищевых продуктов и т. д. Возрастает использование алюминия при строительстве жилых и общественных зданий, сооружений, мостов и т. д. Широко применяют алюминий для защиты поверхности металлов от коррозии, при изготовлении полупроводниковых приборов, в радиолокации, электротехнике, ядерной технике.
Высокоуглеродистая сталь: марки, свойства, состав, применение
Высокоуглеродистая сталь по причине ряда неоспоримых достоинств, которыми она обладает, успешно применяется для производства изделий, использующихся во многих отраслях промышленности. Между тем использование сталей данной категории не всегда целесообразно, поэтому очень важно хорошо разбираться в свойствах и качественных характеристиках подобных сплавов.
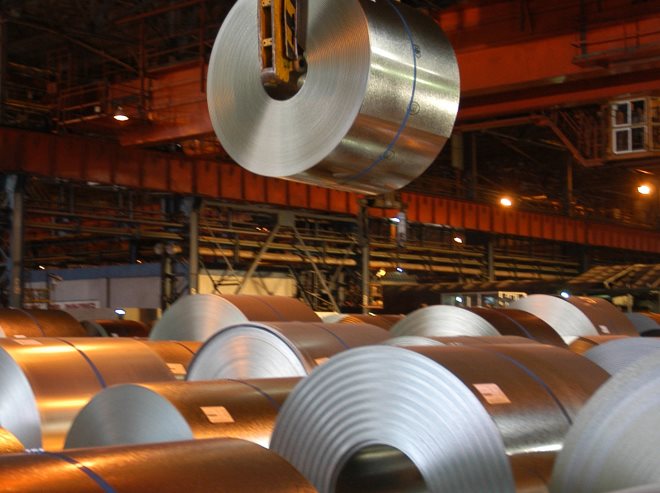
Производство высокоуглеродистой стали
Особенности материала
Любая сталь, как известно, является сплавом железа и углерода, в который могут добавляться различные легирующие элементы. Разделение сталей на мало-, средне- и высокоуглеродистые типы зависит от того, в каком количестве в их составе присутствует углерод. Данный элемент, который оказывает серьезное влияние на характеристики готового сплава, может содержаться в сталях от 0,02 до 2,14%. В сталях, относящихся к категории высокоуглеродистых, количество данного элемента в составе начинается с отметки 0,6%.
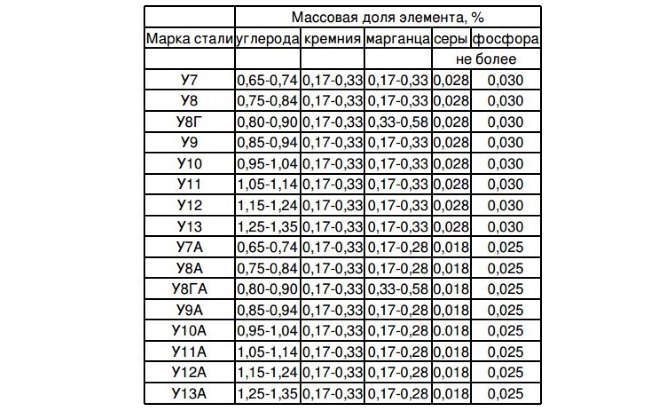
Марки стали и доля различных элементов в их составе
Одной из отличительных особенностей, которой обладают высокоуглеродистые стали, является то, что изделия из них плохо поддаются сварке, ее выполнение приводит к тому, что в зоне сварного шва возникают трещины. Объясняется это тем, что такие материалы, обладая определенным химическим составом, имеют склонность к образованию закаленных зон в тех местах, где металл подвергается термическому воздействию.
В связи с такой особенностью высокоуглеродистых сталей, выполнять сварку изделий из них стоит только при помощи электродов, обладающих невысокой тепловой мощностью. Сварочная дуга, с использованием которой выполняется соединение изделий из высокоуглеродистых сталей, должна быть восстановительного типа. Применение окислительной дуги в таких случаях приведет к тому, что из состава стали будет выжигаться углерод, и, как следствие, металл в области сварного шва станет более пористым. Между тем такого отрицательного эффекта можно избежать, если предварительно прогреть соединяемые изделия до температуры 200–2500.
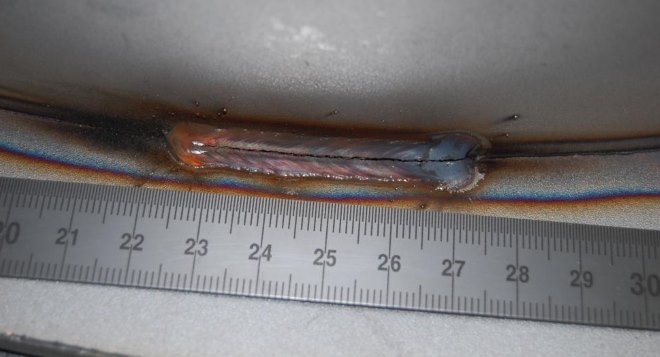
Нарушение технологических особенностей сварки высокоуглеродистых сталей приводит к дефектам сварочного шва
Нержавеющая арматура для пищевой промышленности. Купить в Санкт Петербурге пищевую арматуру
Нержавеющая арматура для пищевой промышленности – это изделия, которые предназначены для использования в тесном контакте с питьевой водой, продуктами питания. Они являются частью трубопроводов, предназначенных для транспортировки жидкостей, а также элементами оборудования, которое используют для измельчения, термообработки, приготовления смесей и сортировки различных продуктов. Сфера применения изделий – производство продуктов питания, водоснабжение жилых домов и других объектов, обеспечение деятельности предприятий фармацевтической и химической промышленности.
Преимущества изделий из нержавеющей стали
Учитывая сферу применения, к изделиям предъявляются повышенные санитарно-гигиенические и эксплуатационные требования по стандартам. Для их производства используют высококачественные сплавы – сталь AISI 316, улучшенную молибденом, а также AISI 304, которая отличается от предыдущей марки меньшей стойкостью к коррозии.
К преимуществам изделий из стальных сплавов относится:
высокая прочность и долговечность;
жаропрочность и устойчивость к коррозии;
устойчивость к лимонной, молочной и другим кислотам;
экологически чистый состав.
Стальная продукция высокого качества
Компания NESDY предлагает качественную пищевую арматуру европейского производства:
соединительные компоненты трубопровода для создания различных его модификаций – соединения приварного, резьбового типа;
запорные и регулирующие элементы для управления технологическим процессом – клапаны, затворы, заслонки.
У нас представлена сертифицированная продукция, которая полностью соответствует санитарно – гигиеническим требованиям и мировым стандартам качества. Товар можно приобрести в любом количестве с доставкой по Санкт – Петербургу и в другие регионы.
Нержавеющие стали для пищевой промышленности
Нержавеющая сталь была изобретена около ста лет назад. На широком рынке ножи из нержавейки, содержащие 12-13% хрома (Cr), появились в 1912 году. Но исследования металлургии и физических свойств этих сплавов проводились еще в 1902 г. Гулле и в 1909 г. Портевеном во Франции, а также Гисеном в 1907 г. в Англии.
Однако «изобретателем» нержавеющих сталей считают инженера Х. Брирли. Он был первым, кто ясно представил промышленные возможности этого материала. Сейчас нержавеющая сталь заняла одно из лидирующих мест среди наиболее значимых материалов в мире.
Класс материалов, объединенных термином «нержавеющие стали», точно не определен, но принято считать, что он включает в себя сплавы, основными составляющими которых являются железо и не менее 12% хрома. Они устойчивы к электрохимической, химической (атмосферной, почвенной, щелочной, кислотной, солевой), межкристаллитной и другим видам коррозии. Увеличение содержания хрома повышает коррозионную стойкость материала. Повышение устойчивости стали к коррозии достигается введением в нее элементов, образующих на поверхности защитные пленки, прочно связанные с основным металлом и предупреждающие контакт между сталью и наружной агрессивной средой. Этот защитный слой очень устойчив и даже после механического или химического повреждения, быстро приобретает свой прежний вид, и антикоррозионные качества металла остаются без изменений.
К хромо-никелевым сталям широко практикуется присадка других элементов (Ti, Nb), которые устраняют склонность к интеркристаллитной коррозии, присадка Si повышает жаростойкость. При изготовлении деталей пищевой промышленности, не подвергаемых термической обработке, желательно применение сталей типа 18-8 с пониженным содержанием углерода (ниже 0,06%), которые не склонны к интеркристаллитной коррозии.
Переработка молока - "Нержавеющие стали в пищевой промышленности"
При изготовлении и эксплуатации оборудования важно иметь представление
о составе и свойствах нержавеющих сталей и об основных причинах возникновения
в них коррозионных процессов.
Взаимодействие системы
«продукт-материал» оценивается и регламентируется
Минздравсоцразвития России с точки зрения охраны здоровья
потребителя. При этом для каждого
вида продукта имеются материалы,
разрешенные или запрещенные к
применению.
Например, медь запрещена к применению в оборудовании молочных
заводов и разрешена к применению
в оборудовании кондитерского производства; алюминий разрешен к
применению в молочной промышленности вообще, но запрещен, в
частности, к применению при производстве молочных продуктов для
детского питания.
Специфика условий пищевого производства (коррозионно-активные
пищевые среды, моющие и дезинфицирующие растворы, повышенная
температура, высокая скорость истечения рабочих сред, значительные
перепады давления) определяет особые требования к выбору материалов при конструировании технологического оборудования. В связи со
всеми этими факторами любые материалы должны быть разрешены
для производства конкретных пищевых продуктов.
Наиболее распространенным материалом для изготовления оборудования пищевого производства является так называемая в обиходе
«нержавейка», т.е. нержавеющая
сталь. Но, к сожалению, даже «нержавеющее» оборудование как при
изготовлении, так и в процессе эксплуатации подвергается коррозии
различного вида. Поверхность емкостного оборудования покрывается
темным налетом, на полированных
поверхностях появляются белесые
серые, до темно-серого и даже фиолетового цвета разводы. Надо заметить, что такое поведение «нержавейки» в настоящее время стало
встречаться все чаще и чаще, и иногда старое оборудование выглядит
лучше, чем новое после непродолжительного времени эксплуатации.
Состав и свойства сталей
Нержавеющие стали – это сложнолегированные стали, стойкие против
коррозии в атмосфере и агрессивных
средах.
Химические элементы, специально
вводимые в сталь для изменения ее
строения и свойств, называются легирующими. Стали, содержащие легирующие элементы, называются легированными.
Основными легирующими элементами являются Cr, Ni, Mn, Si, W, Mo,
V, Al, Cu, Ti, Nb, Zr, B. По количеству
легирующих элементов различают
низколегированные стали, содержащие до 2,5 %, среднелегированные –
от 2,5 до 10 % и высоколегированные – более 10 % легирующих элементов. Введение в нержавеющие сплавы
вышеуказанных легирующих элементов позволяет получить различные
виды кристаллической решетки, что
дает возможность добиться различных свойств стали.
Нержавеющие стали, принадлежащие к средне- и высоколегированным
группам, представляют собой хромсодержащие сплавы. Коррозионная
стойкость этих сталей в значительной степени объясняется наличием
хрома, обладающего способностью
пассивироваться, тем самым создавать защитный слой на поверхности
металла. Минимальное содержание
хрома в стандартной нержавеющей
стали не менее 10,5 %. С увеличением
количества хрома в сплаве увеличивается его коррозионная стойкость.
Для изготовления пищевого оборудования, например, в виноделии,
пивном, дрожжевом производстве,
хлебопечении и др., рекомендуются
хромистые стали, с содержанием
хрома не менее 17 %. Использование
сталей с содержанием хрома 13 –
14 % для пищевых производств не
рекомендуется из-за низкой их коррозийной стойкости. Такие стали во
влажно-воздушной среде корродируют с образованием окиси железа.
Хромистые сплавы устойчивы для
тех сред, в которых они пассивируются и в которых не разрушается их
защитная пленка. Для повышения
коррозионных свойств в систему
сплава железо – хром добавляют никель, во избежание межкристаллитной коррозии сварных швов и зоны
нагрева в диапазоне 450 – 850 ?C
вводится титан, а для предотвращения точечной коррозии вводится молибден.
Нержавеющие стали кроме коррозионных свойств должны обладать и
другими специфическими свойствами – пластичностью, вязкостью,
прочностью, гибкостью, хорошей
пригодностью к сварке.
Наряду с введением легирующих
элементов для изменения или стабилизации полученных свойств стали
подвергают различного вида термическим обработкам, в связи с чем,
применение повышенных температур, как в процессе изготовления, так
и эксплуатации оборудования, может
изменению свойств металла.
В зависимости от введенных легирующих элементов и проведенных
термообработок различают четыре
основных вида нержавеющих сталей:
аустенитные, ферритные, аустенитноферритные и мартенситные.
Аустенитная сталь является самым распространенным типом нержавеющей стали, применяемой при
изготовлении пищевого оборудования. Эта сталь легируется никелем,
(не менее 7 %), титаном, молибденом, марганцем, что придает ей пла-
стичность, широкий спектр температурных режимов, немагнитные
свойства и хорошую пригодность к
сварке. Именно этот тип нержавеющей стали и должен использоваться
при изготовлении пищевого оборудования.
По назначению различают три
группы сталей: конструкционные
(машиностроительные и строительные), инструментальные (штамповые,
для режущего и измерительного инструмента) и с особыми физическими
и химическими свойствами (коррозионностойкие, жаропрочные, элек-
тротехнические, магнитные и др.).
Коррозия: виды и причины
Разрушение металла под действием
окружающей среды называется коррозией. Коррозия обычно начинается
с поверхности металла и при дальнейшем ее развитии распространяется вглубь, вызывая изменение состава металла и его свойств.
Металл при этом частично либо
полностью разрушается, либо же
продукты коррозии могут образоваться в виде осадка на поверхности
металла. Скорость коррозии металлов в значительной степени зависит
от характера воздействующей среды.
Процессы коррозии по-разному протекают в кислых, щелочных и нейтральных средах, при повышении
температуры коррозионные процессы активизируются, одновременное
воздействие агрессивной газовой
(воздушной) среды и повышенных
температур приводит к интенсивному образованию продуктов корро-
зии и, соответственно, изменению
свойств металла и внешнего вида
оборудования.
В зависимости от характера коррозионного разрушения коррозия мо-
жет быть равномерной (сплошной)
или неравномерной, т. е. сосредоточенной на отдельных участках.
Если коррозия вызывает разрушения только некоторых участков ме-
талла, а остальная часть поверхности
остается незатронутой, то такой вид
коррозии называют местной. Различают следующие виды местной кор-
розии:
1) коррозия пятнами – разрушения
на отдельных участках распространяются в виде пятен на небольшую глу-
бину; такое разрушение более близко
к равномерной коррозии;
2) коррозия в виде язв – углубления
в металле, сосредоточенные на сравнительно ограниченных участках;
3) точечная коррозия – глубокие
местные разрушения в виде точек,
которые могут перейти в сквозные;
4) подповерхностная коррозия –
разрушения, которые начинаются на
поверхности металла и затем переходят под поверхность; продукты
коррозии сосредотачиваются под
ней, вызывая вспучивание и расслоение металла;
5) избирательная коррозия – разрушает только одну структурную составляющую или один компонент
сплава;
6) межкристаллитная коррозия – ее
также можно отнести к избирательной коррозии, характеризующейся
разрушением металла по границам
кристаллитов;
7) транскристаллитная коррозия –
в отличие от межкристаллитной,
здесь коррозионные разрушения
распространяются в глубь металла
по телу кристаллитов;
8) коррозионное
растрескивание.
Равномерная
коррозия представляет собой
один из наименее
опасных видов
коррозии, чаще
всего равномерная
коррозия не вызывает значительного разрушения металла, тем не менее
она может быть
нежелательной по причине потускнения или изменения цвета металла.
Различные виды местной коррозии
происходят в случаях неполной пассивности металла, при неравномерной аэрации углублений, различной
концентрации раствора в разных
точках, при неоднородной обработке
металла.
При точечной коррозии на отдельных участках конструкций или обо-
рудования могут образоваться раковины и сквозные отверстия. Точечная
коррозия особенно типична для пассивирующихся металлов (хром, алюминий, хромоникелевые стали) и возникает в результате нарушений в отдельных участках пассивирующего
слоя, который покрывает поверхность стали и предотвращает возник-
новение коррозии.
Точечную коррозию стали так же
могут вызывать компоненты сталелитейного процесса металлургиче-
ского производства – сульфиды. Исследования показали, что причиной
такой коррозии является сера, которая имеет более низкую температуру плавления, чем сталь, и, во время
литья, в течение короткого времени
после того, как сталь укрепилась, попадает в структуру поверхности металлических листов прокатной ста-
ли. Эти частицы примеси «всасывают» хром из структуры стали,
создавая области (точки) слабости
на поверхности нержавейки. Как
только подобные соединения достигают внешней поверхности металла,
эта область может быть подвержена
коррозии точно также как и железо.
Именно поэтому нержавеющая сталь
– не столь идеальная «нержавейка»,
как принято считать. Существенное
влияние на скорость развития точечной коррозии так же оказывают
степень чистоты металла и повышение температуры.
Межкристаллитная коррозия
очень опасна вследствие разрушения
металла по границам кристаллитов.
Часто межкристаллитная коррозия
не изменяет внешнего вида металла,
и разрушение оборудования или детали может произойти неожиданно.
При сварке высоколегированных сталей в ряде случаев наблюдается так
называемая ножевая коррозия. Опасность возникновения такой коррозии
особенно велика в зонах сварного
шва. Режим сварки нержавеющих
сталей должен быть таким, чтобы
участки стали у шва не попадали в область действия опасных температур
450 – 850 ?C, так как в этом интервале и при последующем медленном
охлаждении происходит обеднение
пограничных участков зерен хромом,
возникает процесс депассивации, в
результате чего коррозионная стойкость стали резко понижается.
Неправильный режим термической
обработки в процессе изготовления
оборудования или термическое воздействие в опасном интервале (свар-
ка, гибка с подогревом и т.д.) вызывает снижение коррозионной стойкости и появление склонности к
межкристаллитной коррозии. Склонность к межкристаллитной коррозии
можно объяснить так же повышенным содержанием углерода в сплаве
и отсутствием титана. Чтобы предотвратить такую коррозию и повысить
общую коррозионную стойкость в
сталь вводят присадку титана в коли-честве, в 6–7 раз превосходящем содержание углерода.
Сварке нержавеющих сталей во
всех странах уделяется много внимания, т. к. сварные швы и околошовная
зона являются наиболее уязвимыми
для коррозии участками. При соблюдении определенных условий удается
производить сварку с сохранением
коррозионной стойкости швов и околошовной зоны. Сварка должна проводиться в среде инертного газа, шов
должен быть ровный, без зазоров,
свищей и расслоений, сам шов и околошовная зона должны иметь только
«цвета побежалости». Наличие
черно-красной окалины говорит о
выгорании легирующих элементов и
исчезновении коррозионной стойкости. В таких случаях необходимо произвести зачистку сварной зоны и шва
и восстановить пассивную пленку химическим путем специальными растворами или пастами.
Часто приходится видеть отечественное оборудование из нержавеющей стали со следами коррозии по
сварным швам, зонам зачистки швов
и различных дефектов поверхности
металла (риски, царапины, вмятины).
Почему пошла коррозия? Ответ вытекает из всего вышеизложенного в процессе зачистки сняли пассивный
слой, а восстановить его или забыли,
или просто не знали, как работать с
«нержавейкой». Когда такое оборудование попадет на производство – вот
тут-то и выявятся все нарушения в
технологии работы с нержавейкой.
Факторы, влияющие
на изготовление
и эксплуатацию
оборудования
Существует много фирм, берущихся за изготовление «нержавеющего»
оборудования, их снабженцы ищут
для него «нержавейку» «подешевле»,
но дешево почти всегда не бывает хорошо. Дешевая «нержавейка» – это,
скорее всего, тот тип стали, в котором
легирующих элементов содержится
минимальное количество, либо их
нет. Плюс к этому – несоблюдение
технологий работ с нержавеющими
сталями при изготовлении оборудования. И вот пищевое предприятие,
установившее такое оборудование,
через некоторое, сравнительно недолгое, время начинает пожинать
плоды – по сварным швам, в местах
зачисток, полировок и в местах гиба
появляется местная коррозия, внешняя поверхность, особенно емкостного оборудования, темнеет, на ней появляются разводы от серого до темно-
фиолетового цвета, пятна и пр.
В пищевой промышленности поверхности оборудования подверга-
ются различному воздействию. Специфика пищевого производства предусматривает целый ряд многократных
санитарно-гигиенических мероприятий с использованием горячей воды,
моющих и дезинфицирующих растворов различной рН, концентрации,
температуры и времени воздействия,
что может спровоцировать на некачественном оборудовании начало
коррозионного процесса, как на наружной, так и на внутренней поверх-
ностях оборудования. При подборе
моющих и де зинфицирующих
средств обязательно должны учитываться материал оборудования и его
физическое состояние (срок эксплуатации, износ и механические повреж-
дения поверхности металла).
Необходимо обратить особое внимание на такой, казалось бы, безо-
бидный фактор, как промывочная вода. Коррозия сталей может возникать
в любой воде – чистой, сверхчистой,
паре, очищенной питьевой воде или
неочищенной технической воде.
Умягчение воды не удаляет анионы,
такие как карбонаты, бикарбонаты,
хлориды и т. п., а только обеспечивает обмен с катионами, такими как
кальций и магний, с содой и калием.
Даже кратковременное воздействие
хлорсодержащих реагентов может
стать отправной стадией появления
коррозии, в особенности если поверхность нержавеющей стали шероховатая.
Полированная стальная поверхность обладает повышенной корро-
зионной устойчивостью, но такие повреждения как царапины, риски,
чистка абразивным материалом или
металлическими щетками приводят
к возникновению коррозии.
59
№ 4 2010 ПЕРЕРАБОТКА МОЛОКА
оборудование ПРО изводство
Механически полированные поверхности имеют более низкую кор-
розионную стойкость, нежели электрополированные поверхности, так
как при полировальных операциях
остаются микроскопические изъявления. Электрополировка удаляет эти
изъявления и производит пассивирующий слой с более высоким соотно-
шением хром- железо. Изъявления образуют элементы коррозии, где могут
концентрироваться растворы хлоридов и продолжать реагировать, даже
если система в целом оснащена промывкой с высокой жесткостью воды.
Использование сильнодействующих
ПАВ в растворе промывки будет способствовать удалению хлоридов. Чер-
ная, но не бурая коррозия, образуется
в присутствии пара и горячей воды,
близкой к температуре пара. При первоначальном образовании она синяя,
а затем становится черной, поскольку
она нарастает до предельной толщины,
предупреждающей
дальнейшее проникновение кислорода. На электрополированных поверхностях нержавею-
щей стали такая коррозия блестящечерная, а на непассивированных
механически полированных поверхностях она может быть матово-черной.
Анализ с использованием фотоэлектронной спектроскопии показывает,
что этот слой является полуторной
окисью железа, обычно именуемой
магнитным железняком. Он не удаляется обычной чисткой, но может быть
удален химическими средствами или
шлифованием. Если коррозия является блестяще черной, то ее можно оста-
вить, так как она достаточно стабильна. Матовый слой коррозии может потребовать чистки, после чего
поверхность должна быть химически
запассивирована, но при последующей
эксплуатации оборудования поверх-
ность может снова потемнеть.
Требования к эксплуатации
оборудования
Несмотря на высокую коррозионную стойкость нержавеющих сталей,
для обеспечения долговечности оборудования, изготовленного из них,
необходимо выполнять следующие
требования:
•• не допускать контакта разнородных металлов (а в случае конструк-
тивной необходимости такого контакта разъединять металлы изоли-
рующими прокладками);
•• аппараты не должны иметь острых
углов, щелей, труднодоступных углублений, способствующих оседанию
твердых частиц и застаиванию сред;
по этой же причине следует избегать
нахлесточных сварных соединений;
•• избегать контакта нержавеющего
оборудования с пористыми материалами, имеющими свойство впиты-
вать среды;
•• избегать длительного контакта с
горячими концентрированными растворами, содержащими хлористый
натрий (поваренная соль), с кислыми
растворами на основе соляной кислоты при любых температурах, дезинфицирующих средств с содержанием хлора;
•• не допускать засыхания пищевых
сред, как кислого, так и нейтрального
характера, на поверхности металла
(нейтральная среда имеет свойство
прокисать);
•• при промывке оборудования, особенно с полированной поверхностью,
применять не горячую, а теплую (25 –
50 ?C) воду;
•• подбирать моющие и дезинфицирующие средства для санитарных обработок оборудования следует с учетом их коррозионного воздействия
на металл (подробную характеристику препаратов, а также технологию их
применения, обязан предоставить
завод-изготовитель);
•• по окончании санитарных обработок необходимо обеспечивать полноту смываемости используемых рас-
творов;
•• при отработке технологий санитарной мойки применять минималь-
но допустимую концентрацию пре-
паратов и минимально требуемую
температуру растворов.
Марки нержавеющих сталей
Легированные (нержавеющие) стали являются сегодня практически не-
заменимым материалом для изготовления пищевого оборудования. Технологическая и санитарно-гигиеническая
оценка нержавеющих сталей, контактирующих с продуктами виноделия
как с наиболее коррозионно-активными,
позволила выявить марки нержавеющих сталей, допущенных к
контакту с пищевыми продуктами.
Детали и узлы, длительно контактирующие с суслом, вином, коньячным
спиртом, продуктами переработки отходов виноделия, в свеклосахарном,
ликероводочном, хлебопекарном, кондитерском производствах – необходи-
мо изготавливать из сталей марок
12Х18Н9Т, 12Х18Н10Т, 08Х21Н6М2Т,
12Х21Н5Т, 10Х14Г14Н4Т, 08Х17Т,
08Х21Н5Т, 08Х18Г8Н2Т в состав которых входит хром, никель, титан. Детали и узлы, непродолжительно контак-
тирующие с суслом и вином – из сталей 12Х13,20Х13, 30Х13, 12Х17,
14Х17Н2. Детали машин, аппаратов и
цистерн для перевозки и хранения вина, коньячного спирта, молочных продуктов – из сталей 08Х18Г8Н2М2Т,
08Х23Н28М2Т, 40Х25Н.
В настоящее время предприятиям,
изготавливающим оборудование, все
чаще предлагаются импортные нержавеющие стали, маркировка которых указывается в соответствии с зарубежными стандартами, чаще всего – Германия – DIN, США – AISI.
Самыми распространенными сейчас являются стали марок AISI 304,
AISI 304L, AISI430, AISI316, AISI-
316Ti, AISI321, которые часто рекламируются как аналоги с т али
08Х18Н10Т, 12Х18Н10Т, Х18Н9Т.
Действительно, все эти стали относятся к легированным нержавеющим
сталям, но стали марок AISI304, AISI430,
AISI316 не стабилизированы
титаном, а значит, подвержены межкристаллитной коррозии и снижению коррозионной стойкости в зонах нагрева: в зонах сварки, пайки,
гибки. Эти зоны необходимо после
механической зачистки подвергать
обязательной химической пассива-
ции специальными пастами или растворами.
Различные термические, механические и химические воздействия на
эти стали как в процессе изготовления, так и в процессе эксплуатации
оборудования, меняют структуру поверхности стали, что делает ее уязви-
мой к воздействию различных рабочих сред пищевого производства и
средств санитарно-гигиенической
обработки. В связи с этим при изготовлении или эксплуатации оборудования, изготовленного из сталей этих
марок, необходимо выполнять вышеуказанные рекомендации.