Особенность российских электрических сетей
10(6) кВ, не имеющих глухого заземления нейтрали, состоит в том, что
они могут некоторое время работать с однофазным замыканием на землю.
При этом изменяются только напряжения отдельных фаз относительно
земли, а треугольник междуфазных напряжений остается неизменным. Это
позволяет потребителям никак не реагировать на наличие замыкания на
землю и продолжать работу в обычном режиме. А электросетевое
эксплуатационное предприятие обязано найти и отремонтировать
поврежденный участок. Выполнение этой задачи во многом зависит от типа
используемых трансформаторов напряжения (ТН).
Применяемые в настоящее время ТН делятся на заземляемые и
незаземляемые. Незаземляемые ТН, в отличие от заземляемых, не имеют
соединений первичной обмотки с землей. Заземляемые ТН, помимо
междуфазных напряжений, могут трансформировать напряжения отдельных
фаз относительно земли и тем самым контролировать изоляцию сети.
Указанное обстоятельство определило сферу использования этих видов ТН в
сетях 10(6) кВ:
незаземляемые ТН преимущественно устанавливаются непосредственно
на стороне высокого напряжения (ВН) силовых потребительских
трансформаторов в ТП 10(6) кВ,
заземляемые – на сборных шинах центров питания (ЦП) и распределительных пунктах (РП).
ТРАНСФОРМАТОРЫ НАПРЯЖЕНИЯ ДЛЯ СЕТЕЙ 6–10 КВ
ПРИЧИНЫ ПОВРЕЖДАЕМОСТИ
Незаземляемые ТН
Такие ТН включаются между фазами сети и бывают либо однофазными
(типа НОЛ, НОМ), либо трехфазными (типа НТМК). Они имеют только одну
вторичную обмотку с наивысшим классом точности 0,2 или 0,5, что вполне
приемлемо для питания коммерческих счетчиков электроэнергии.
При этом следует помнить, что класс точности ТН гарантируется только
при определенных условиях эксплуатации. В частности, фактическая
нагрузка при cosj = 0,8 должна быть симметричной и находиться в
пределах от 25 до 100% от номинальной мощности. Если фактическая
нагрузка меньше 25%, что характерно для применения электронных
счетчиков с малым потреблением, то ее следует искусственно увеличить.
Если же она больше 100%, то ТН переходит в низший класс точности.
Классы точности гирь: E1, E2, F1, F2, M1, M1-2, M2, M2-3, M3, их поверка и калибровка
Для определения массы предметов на предприятиях, в лабораториях , а также в торговых заведениях используются различное весовое оборудование.
Для проведения таких измерений, а также калибровки и поверки весов используются гири. Основные требования к техническим характеристикам измерительных гирь и методам их проверки приведены в соответствующем стандарте.
Классы гирь и их применение
Всего имеется 7 классов точности гирь.
Каждый из этих классов имеет свою точность и другие характеристики. Применение гирь зависит от этих параметров, а именно:
класс Е1 предназначен для проверки гирь класса Е2 и более низких классов; класс Е2 предназначен для проверки гирь класса F1 и взвешивания на весах высшей точности 1 класса; класс F1 предназначен для проверки гирь класса F2 и взвешивания на весах 1 и 2 классов; класс F2 предназначен для проверки гирь класса М1 и использования с весами высокой точности 2 класса; класс М1 предназначен для проверки гирь класса М2 и применения с весами 3 класса; класс М2 предназначен для проверки гирь класса М3 и взвешивания на весах 3 класса; класс М3 предназначен для использования с весами средней точности 3 класса; классы М1-2 и М2-3. К этим классам относятся гири низкого класса массой от 50 до 5000 кг, предназначенные для использования с весами средней точности.
При выборе класса точности гири для проверки весов необходимо учитывать, что погрешность гири не должна быть больше 1/3 погрешности весов .
Конструкции гирь
Гири размерами 1 г и меньше должна иметь вид плоских многоугольников или вид проволоки. При этом гири массой 5, 50 и 500 мг должны иметь вид многоугольника, 2, 20 и 200 мг — квадрата, а 1, 10, 100 и 1000 мг – треугольника. Для гирь от 1 г до 50 кг чаще используют форму цилиндра или конуса. Высота гири должна составлять от 3/4 до 5/4 величины ее диаметра. Кроме того, гиря может иметь отвинчивающуюся головку.
» Марки бетона по прочности
Вопрос о качестве и прочности бетонанеизменно возникает в процессе его выбора и покупки. По мере развития технологий создавался весьма обширный ассортимент марок этого строительного материала.
Каждый вид бетона предназначен под конкретные условия его использования. Есть более универсальные растворы или для специальных задач.
Критерии
Определяющим показателем при покупке бетонной смеси являются условия и задачи ее использования. Для бетонных растворов существует два классифицирующих обозначения – марка и класс. Они информируют покупателя о свойствах строительного материала. Первая – это значение средней прочности, а второй — гарантировано обеспеченная прочность, которая обозначает, что свойства бетонных изделий обеспечиваются в 95 и больше случаях из 100.
Марка и класс определяется значениями:
стойкости к сжатию (проектная, марочная);
морозоустойчивости, воздействия высоких температур, влагонепроницаемости.
Марка
Этот индекс обозначается в цифровом значении и буквой М. Существует обширный перечень марок бетона марок от 50 до 1000, наиболее часто используется около десятка. Для свойств бетона определяющими условиями являются количество и качество цементной смеси в составе порошка. Марка зависит от расчетной прочности на сжатие — это значение в кгс/см2 на момент затвердевания раствора (на 28 день).
Чем больше цифра в индексе, тем бетон прочнее. Это значит, что он имеет больше цемента лучшего качества. Такой бетон дороже. Поэтому основная задача при выборе – найти баланс между ценой и требуемыми свойствами при возведении конкретного сооружения.
С раствором высокой прочности труднее работать – смесь быстрее сохнет, а это чревато последствиями при медленной работе: доставлять раствор и работать с ним нужно быстрее.
7.3. Методы повышения конструкционной прочности
Высокая прочность и долговечность конструкций при минимальной массе и наибольшей надежности достигаются технологическими, металлургическими и конструкторскими методами.
Наибольшую эффективность имеют технологические и металлургические методы, цель которых - повышение механических свойств и качества материала.
Из механических свойств важнейшее - прочность материала, повышение которой при достаточном запасе пластичности и вязкости ведет к снижению материалоемкости конструкции и в известной степени к повышению ее надежности и долговечности.
Прочность - свойство, зависящее от энергии межатомной связи, структуры и химического состава материала. Энергия межатомного взаимодействия непосредственно определяет характеристики упругих свойств (модули нормальной упругости и сдвига), а также так называемую теоретическую прочность.
Модули нормальной упругости и сдвига являются константами материала и структурно нечувствительны.
Теоретическая прочность (сопротивление разрыву межатомных связей) в реальных кристаллах из-за наличия структурных дефектов не достигается. Реальная прочность на два-три порядка ниже теоретической и определяется не столько межатомными силами связи, сколько структурой материала.
В гл. 4 указывалось, что уровень прочности (сопротивление пластической деформации) зависит главным образом от легкости перемещения дислокаций. В связи с этим современные методы повышения прочности материала основаны на создании такого структурного состояния, которое обеспечивало бы максимальную задержку (блокировку) дислокаций. Методы упрочнения рассмотрены в предыдущем разделе. Напомним, что к ним относятся легирование, пластическая деформация, термическая, термомеханическая и химико-термическая обработка. Повышение прочности указанными методами основано на ряде структурных факторов.
Различия болтов ГОСТ 7805-70 и ГОСТ 7798-70
Метрический крепёж (в который входят болты, гайки, винты, шайбы) является составной частью крепёжных изделий. Болты с шестигранной головкой имеют ГОСТы 7805-70 и 7798-70. При этом существует 4 варианта их исполнения, а также разные классы точности.
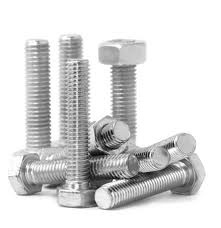
Болты, изготовленные по ГОСТам 7805-70 и 7798-70 1-го и 4-го исполнения не содержат отверстий. В болтах исполнения 2 и 3 имеются сквозные отверстия, как в резьбовой части стержня, так и в головке. ГОСТы предписывают следующие параметры и конструкцию болтов: диаметры стержней, диаметр резьбы, диаметры отверстий в болтах, а также размеры "под ключ". Болты отечественного производства подразделяются на классы точности:
Класс А – повышенный класс точности.
Класс В – нормальная точность.
Класс С – грубая точность.
ГОСТы 7805-70 и 7798-70 распространяются только на болты, которые имеют класс точности А или В.
ГОСТ 7805-70 описывает болты класса точности А, имеющие диаметр резьбы до 48 мм. Так, по данному стандарту болт исполнения 2 имеет одно отверстие в резьбовой части стержня. При этом размер диаметра отверстия варьируется, начиная с 1.0, 1.2 … и т.д. до 8.0 мм. Болт исполнения 3 того же стандарта имеет радиальное отверстие различных диаметров: 1.0, 1.2, 2.0, … 5.0 мм. При диаметрах резьбы от 36 мм до 48 мм выпускают болты с резьбой с шагом 2 мм. ГОСТ 7805-70 предписываетизготавливать болты из нержавеющей аустенитной стали (марки А2 и А4 с классами прочности 50, 70 и 80) и из углеродистой стали. При этом рекомендуется изготавливать изделия с прочностью класса 4.8, 5.6, 5.8, 6.8, 8.8 или 10.9.
Болты с классом точности В и размером диаметра резьбы от 6 мм до 48 мм описывает ГОСТ 7798-70 . Как и в предыдущем стандарте болты исполнения 2 имеют одно отверстие в резьбовой части стержня, однако согласно ГОСТ 7798 -70 диапазон размеров диаметров более узкий: 1.6, 2.0, 2.5,…, 8.0 мм.
Болты исполнения 3 имеют три радиальных отверстия в головке с диапазоном диаметра от 2 до 5 мм. Болты производятся из углеродистой стали, которая имеет класс прочности 4.8, 5.8, 8.8 или 10.9).
Болты в ГОСТах 7805-70 и 7798-70 отличаются по классам точности и диапазонам диаметров и длин. Основная разница между ними в том, что ГОСТ 7805 распространяется только на болты, имеющие класс точности A, а ГОСТ 7798 – на болты класса точности B. В большинстве сборочных производств заводовна текущий момент хватает нормальной точности болтов, поэтому болт ГОСТ 7798-70 более востребован и популярен, к тому же он немного дешевле обходится при его изготовлении.
Расшифровка сталей, сплавов и чугунов: таблица, примеры. Расшифровка сталей по составу
Сталь – сплав железа и углерода, содержание которого не превышает 2,14%. Обладает высокой ковкостью и прокатываемостью, чем обусловлено его широкое применение в промышленности, машиностроении и в других отраслях.
В металлургическом производстве, где прокат отличается не только профилем, но и марками стали, маркировка каждой штуки прокатанных изделий давно стала непременным правилом. Расшифровка сталей дает возможность сразу сделать вывод о применимости данного металла для той или иной технологической операции или для конкретного изделия вообще.
Маркировка наносится на торец каждой единицы профилей методом "горячего клейма" в потоке производства так называемыми клеймовочными машинами. Маркировка содержит: марку стали, номер плавки, клеймо производителя. Кроме того, каждая заготовка маркируется несмываемой краской в комбинации цветов по группам сталей на остывших заготовках. По соглашению сторон, цветовая маркировка может наноситься на отдельные профили в пакете в количестве 1-3 штук на пакет. Пакет – связка профилей общим весом 6-10 тонн, упакованная обвязкой из катаной проволоки диаметром 6 мм в 6-8 ниток.
Стали легированные
Таблица расшифровки сталей по составу представлена ниже.
Обозначение
Хим. элемент
Наименование
Обозначение
Хим. элемент
Наименование
Х
Cr
Хром
А
N
Азот
С
Si
Кремний
Н
Ni
Никель
Т
Ti
Титан
К
Co
Кобальт
Д
Cu
Медь
М
Mo
Молибден
В
Wo
Вольфрам
Б
Nb
Ниобий
Г
Mn
Марганец
Е
Se
Селен
Ф
W
Ванадий
Ц
Zr
Цирконий
Р
B
Бор
Ю
Al
Алюминий
Если в названии имеется буква "Ч", значит в состав легирующих элементов входят редкоземельные элементы – ниобий, лантан, церий.
Церий (Ce) – оказывает влияние на прочностные характеристики и пластичность.
Лантан (La) и неодим (Ne) – снижают содержание серы и уменьшают пористость металла, приводят к уменьшению зернистости.
Прочность щебня
Щебень производится из большого разнообразия видов скальных, горных пород, некондиционных отходов рудных предприятий, попутно добываемых материалов, неметаллических ископаемых, гравия и валунов природных карьеров.
Его производство заключается в измельчении сырья в дробильных установках и рассеивании получаемого продукта по фракциям крупности. Щебень применяют в основном в строительных сферах производства, поскольку аналогичный по виду и составу материал, используемый в других областях, называется иначе — флюсы для металлургии, сырье для обжига извести и т. д.
Качество такого материала оценивают по основным параметрам устойчивости к воздействиям, испытываемым при применении. К ним относятся:
прочность при сжатии; износостойкость на истирание; морозостойкость.
Высокая прочность щебня при сжатии требуется в бетонных конструкциях фундаментов высотных зданий, башен, в нагруженных опорах мостов, в мощных гидротехнических сооружениях.
Износостойкость становится важнейшим показателем прочности щебня в асфальтобетонных покрытиях, испытывающих истирающие нагрузки от колес большегрузного транспорта.
От морозостойкости, не являющейся прямым прочностным параметром, напрямую зависит долговечность и прочность щебня — основного компонента бетона, асфальтобетона, железнодорожных насыпей и других сооружений.
Марки
Прочность щебня оценивается марками дробимости при сжатии (раздавливании) испытуемой порции в цилиндре. Шкала в порядке убывания прочности выглядит следующим образом: М1400, М1200, М1000, М800, М600, М400 и М200.
Самому прочному щебню присваивают марку М1200-М1400 (высокопрочный), прочному — М800-М1200, средней прочности — М600-М800, низкой — М300-М600, очень низкой — М200.
Для материала, используемого в асфальтобетонных покрытиях, важен второй показатель прочности — на истирание. Марки, определяющие истираемость щебня или гравия, представлены рядом (в порядке увеличения истираемости) от И1 до И4.
Морозостойкость устанавливается присвоением соответствующей марки из ряда (по увеличению стойкости): от F15 до F300, F400.
Самым стойким к механическим нагрузкам считается гранитный щебень, марка прочности которого соответствует М1200 и М1400. Прочность щебня гравийного несколько ниже — М800 – М1200. Прочность известнякового щебня соответствует маркам М400-М800.
Шероховатость поверхности (чистота обработки). Основные понятия, обозначения на чертежах
МЫ В СОЦ.СЕТЯХ:
Навигация по справочнику TehTab.ru:
главная страница / / Техническая информация / / Технологические понятия и чертежи / / Символы и обозначения оборудования на чертежах и схемах. / / Шероховатость поверхности (чистота обработки). Основные понятия, обозначения на чертежах
Шероховатость поверхности (чистота обработки). Основные понятия, обозначения на чертежах.
Базовая длина - длина базовой линии l, длина линиии, используемой для выделения неровностей.
Средняя линия - средняя линия профиля (m-на рисунке), линия, имеющая форму номинального профиля, с минимальным среднеквадратическим отклонением профиля, от этой линии и отсчитывают все числовые значения для шероховатости:
Рисунок. Профиль шероховатости поверхности и обозначения его характеристик. Средняя линия профиля - не обязательно прямая, см. определение выше.
Параметры шероховатости поверхности Ra, Rz, R max, Sm, S, tp описаны в табличке ниже:
Условное обозначение параметра шероховатости
Наименование параметра шероховатости
Определение параметра шероховатости +См. рисунок выше
Ra
Среднее арифметическое отклонение профиля
Среднее арифметическое абсолютных значений (значений по модулю) отклонений профиля в пределах базовой длины. Интегральная величина.
Rz
Высота неровностей профиля по 10 точкам
Сумма средних арифметических абсолютных отклонений точек пяти наибольших минимумов и пяти наибольших максимумов профиля в пределах базовой длины.
Rmax
Наибольшая высота поверхностей профиля
Расстояние между линией выступов профиля и линией впадин профиля в пределах базовой длины.
Sm
Средний шаг неровностей профиля
Среднее арифметическое значение шага неровностей профиля в пределах базовой длины.
S
Средний шаг неровностей профиля по вершинам
Среднее арифметическое значение шага неровностей профиля по вершинам в пределах базовой длины.
tp
Относительная опорная длина профиля
Отношение опорной длины профиля к базовой длине, где "p" - значение уровня сечения профиля.
Если Вам встретился класс шероховатости, то используйте таблицу ниже:
Справочник ГОСТов ГОСТ 16523-89
ГОСТ 16523-89: Прокат тонколистовой из углеродистой стали качественной и обыкновенного качества общего назначения
Технические условия
Technical Requirements
Для тонколистового горячекатаного и холоднокатаного проката из углеродистой стали качественной и обыкновенного качества общего назначения, изготовляемого шириной 500 мм и более, толщиной до 3,9 мм включительно.
Прокат подразделяют:
по способу производства:
горячекатаный,
холоднокатаный;
листы,
рулоны;
холоднокатаный: особо высокой отделки - I,
высокой отделки - II,
повышенной отделки - III (IIIа, IIIб);
горячекатаный: повышенной отделки - III,
обычной отделки - IV;
глубокой - Г,
нормальной - Н.
по видам продукции:
по минимальному значению временного сопротивления ( В ) на группы прочности: К260В, К270В, К300В, К310В, К330В, К350, ОК360В, ОК370В, К390В, ОК400В, К490В;
по нормируемым характеристикам на категории: 1, 2, 3, 4, 5, 6;
по качеству отделки поверхности на группы:
по способности к вытяжке (холоднокатаный прокат толщиной до 2 мм групп прочности К260В, К270В, К310В, К330В, К350В):
В части сортамента прокат должен соответствовать требованиям ГОСТ 19903 горячекатаный, ГОСТ 19904 холоднокатаный.
Прокат изготовляют:
из углеродистой стали обыкновенного качества групп прочноcти ОК300В, ОК360В, ОК370В, ОК400В;
из углеродистой качественной стали групп прочности К260В, К270В, К310В, К330В, К350В, К390В, К490В.
Марки стали и требования к химическому составу для каждой группы прочности приведены в таблице 1.
Таблица 1
Используемые марки стали и требования к химическому составу
Группа прочности
Марки стали
Массовая доля элементов и предельные отклонения, %
К260В
08кп
По ГОСТ 1050
Быстрорежущие инструментальные стали
Из группы высоколегированных сталей для изготовления режущих инструментов используются быстрорежущие стали с высоким
содержанием вольфрама, молибдена, кобальта, ванадия.
Современные быстрорежущие стали можно разделить на три группы.
К сталям нормальной теплостойкости относятся вольфрамовые Р18, Р12, Р9 и вольфрамомолибденовые Р6М5, Р6М3, Р8М3. Эти стали имеют твердость в закаленном состоянии 63...66 HRC, предел прочности при изгибе 2900...3400 МПа, ударную вязкость 2,7... 4,8 Дж/м2
и теплостойкость 600...650 °С. Указанные марки сталей получили наиболее широкое распространение при изготовлении режущих инструментов.
Они используются при обработке конструкционных сталей, чугунов, цветных металлов, пластмасс. Иногда применяются
быстрорежущие стали, дополнительно легированные азотом (Р6АМ5, Р18А и др.). Легирование азотом повышает режущие свойства инструмента на 20...30 %, твердость - на 1- 2 единицы HRC.
Стали повышенной теплостойкости характеризуются повышенным содержанием углерода — 10Р8МЗ, 10Р6М5;
ванадия — Р12ФЗ, Р2МЗФ8, Р9Ф5;
кобальта — Р18Ф2К5, Р6М5К5, Р9К5, Р9К10, Р9М4К8Ф
и др.
Твердость сталей в закаленном состоянии достигает 66...70 HRC, они имеют более высокую теплостойкость (до 620...670 °С).
Это дает возможность использовать их для обработки жаропрочных и нержавеющих сталей и сплавов, а также конструкционных сталей
повышенной прочности и закаленных. Период стойкости инструментовиз таких сталей в 3—5 раз выше, чем из сталей Р18, Р6М5.
Стали высокой теплостойкости характеризуются пониженным содержанием углерода, но весьма большим количеством легирующих элементов — В11М7К.23, В14М7К25, ЗВ20К20Х4Ф. Они имеют твердость 69...70 HRC, и теплостойкость 700....720 °С.
Основные свойства и марки строительных сталей.
Строительная сталь – это разновидность сплава железа с углеродом, предназначенная для изготовления строительных конструкций, арматуры и литых изделий. Она обладает оптимальным составом для того, чтобы выдерживать значительные расчетные нагрузки. Использовать, например, инструментальную сталь для изготовления строительной балки нецелесообразно – даже при аналогичных размерах ее технические характеристики не будут удовлетворять расчётным нормативам.
Классификация

Требования к сталям строительным регламентирует ГОСТ 27772-88* «Прокат для строительных стальных конструкций». Документ определяет сортамент сплавов, приводит классификацию, правила производства, приёмки и применения металла.
Согласно ГОСТ, стали делятся на 2 основных вида по составу:
Углеродистые.
Легированные.
Углеродистые
Количество химического элемента углерода определяет прочность стальной конструкции. Чем его больше, тем крепче металл. Углеродистые сплавы делятся на 3 группы:
Строительные низколегированные стали с содержанием углерода менее 0,25%;
Среднеуглеродистые содержат 0,25-0,60% углерода;
Высокоуглеродистые имеют в составе более 0,60% химического элемента.
Применяются металлы с разным количеством углерода в изготовлении строительных конструкций нормальной напряженности.
Легированные
Для повышения прочности в сплав железа вводят различные металлы в разных количествах. Этот процесс называется легирование. По количеству добавок различают 3 группы сплавов:
Низколегированная – до 2,5% дополнительных металлов;
Среднелегированная – около 2,5-10% добавок;
Высоколегированная – более 10% примесей.
Строительные стали с добавками (легированные) считаются наиболее качественными, чем углеродистые. Они применяются для изготовления ответственных конструкций в строительстве, в космической отраслях, в машиностроении и на железной дороге.
Выбор типа стали определяется ГОСТом и конструктивными расчётами.